World leader in ultrasonic spray fluxing for printed circuit board manufacturing
Sono-Tek is the originator of ultrasonic spray fluxing for wave solder fluxing. The SonoFlux name is an industry standard for ultrasonic spray fluxing around the world, replacing inefficient spray and foam fluxers and improving fluxing processes for wave solder manufacturers with dedicated lines, high mix product, and everything in between. Sono-Tek has won industry awards and accolades for our fluxing systems for quality and excellence in electronics manufacturing from companies such as Ford Motor Company and AT&T since 1990, and we continue to expand and improve our SonoFlux product line today.
SonoFlux EZ – Economical reciprocating ultrasonic spray fluxing system for medium to high mix lines.
SonoFlux Servo – Fully automated reciprocating system with selective fluxing capability.
SonoFlux 2000F – Stationary ultrasonic spray fluxing system for low mix/dedicated lines (available in 300mm or 610mm configurations).
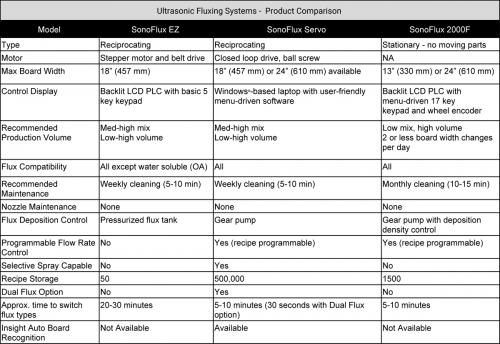
All SonoFlux Systems feature:
- Compatible with ALL fluxes.
- Up to 80% reduction in flux consumption.
- Reduced wasteful overspray and atmospheric contamination.
- Minimal servicing and downtime.
- Self-cleaning ultrasonic nozzle prevents clogging with no moving parts to replace.
- Excellent through hole penetration for maximum top-side fill.
- Selective area capability on multiple models.
- Several models available, including internal, standalone, stationary, and reciprocating.
Sono-Tek uses the ECD Fluxometer to test edge-to-edge coverage and through-hole penetration. Find out more about ECD test pallets by visiting their website: http://www.ecd.com/process-test-pallets/fluxometer.aspx
SonoFlux Servo
Your fluxer is great. It has exceeded all expectations.Bose – New England